Business Process Re-Engineering
Business Process Re-engineering (BPR) is a structured and disciplined approach that seeks to change your business processes in order to improve the performance of your organisation in the areas of service, quality cost and speed. BPR also enables you to re-build your processes for agility and increase your flexibility for change. It enables ownership and accountability to be aligned to strategic performance and objectives. It standardises and simplifies your work and importantly creates a repository of core business knowledge reducing risk around key people dependency.
In this article, we will explore the nature of BPR, the tools and techniques BPR projects typically use and outline some fundamental issues to think about if you are embarking on BPR initiatives.
The Nature of BPR
Business Process Reengineering is about step change, not incremental change. It demands that an organisation review its fundamental purpose and strategy and move from a vertical product focused structure to a horizontal customer focused modus operandi. Instead of focusing on incrementally improving an existing process the effort and energy is put into creating a new / more effective process supported by technology. All biases, ingrained assumptions and existing rules (that no one questions) are rigorously challenged so real improvements and transformation can take place. As Michael Hammer wrote in the Harvard Business Review “Don’t automate, Obliterate”.
Pace of Change
The rate of change is accelerating. Recently Covid-19 has forced fundamental changes for organisations across the world, accelerating digital transformation and introducing new ways of working in some cases overnight. This type of change exposes waste at every level in every organisation, regardless of whether or not the organisation can recognise it. It is at times like this that strategic change is required. Organisations must change and adapt or they will not survive. Nine out of every ten Fortune 500 businesses in the past 60 years have ceased, merged or contracted, demonstrating the pace of disruption which is only accelerating. Previously giants like Nokia and Kodak have felt change sharply through inability to recognise and organise for change.
At the heart of process re-engineering are a number of methods and tools that bring a structured and systematic focus to re-engineering to improve the customer experience, reduce process error and variability and eliminate waste through designing and building new, more effective processes that deliver on customer experience and strategic objectives.
All process re-engineering and improvement should be approached using the Lean Pull principle, in that all efforts must align to the organisations strategic objectives or else risk improving things that don’t matter at the time.
Now let’s introduce some of the tools you can use to challenge your status quo and be ready for change!
Lean Six Sigma
Lean Six Sigma is a proven effective combination of methods and tools from Lean and Six Sigma that focus on standardisation and simplification of processes through waste removal, improvement of efficiency and effectiveness, improving customer experience, reduce costs and increase capacity which in times of big change can make the difference by designing your future change capable processes with process re-engineering
Lean’s simple idea is to maximise value for your customers while minimizing waste (lean.org). Lean is more than a methodology or tools though, it is a way of thinking, a cultural change for your organisation, a foundational part of operational excellence. Lean is about removing the complexity that kills the velocity of your business processes. Lean identifies 8 types of waste and inefficient activities in processes activities as non-value for removal that will lead to designing and building your future state processes that align your people, processes and systems for customer value.
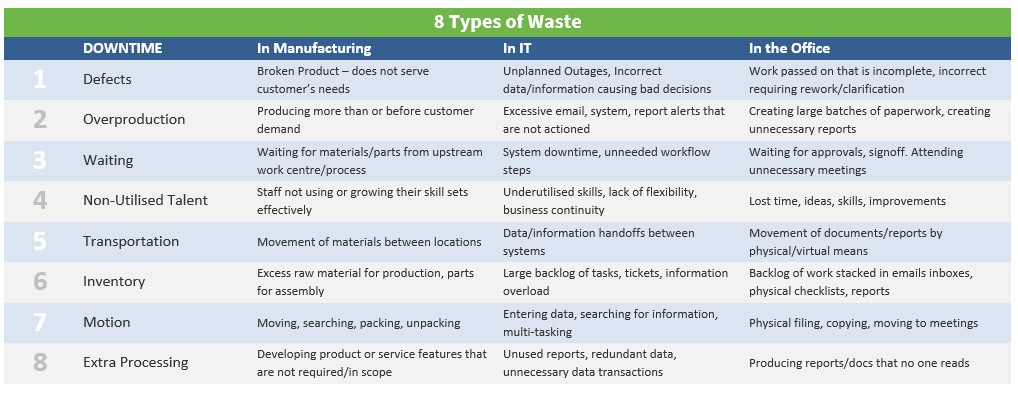
Kaizen
Kaizen meaning “change for the better” on a continuous improvement basis is often seen and experienced through intensive workshops where known business problems are solved rapidly and change is implemented. It focusses on defining customer value and mapping the value stream to identify and remove waste and non-value adding activity.
The Kaizen approach generally contains the following steps:
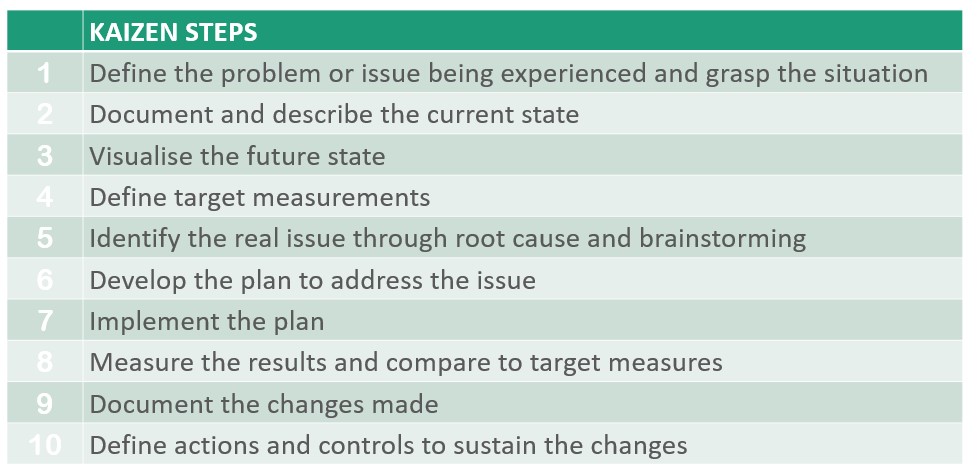
A kaizen event can last from as little as one day to a few weeks long depending on the issues to be addressed. Key considerations for planning and holding a kaizen event are:
- Senior management commitment and understanding of the need
- Clear scope, boundaries and definition of the purpose of the Kaizen
- Be positive and focus on what can be done
- Clear communication to the whole organisation about the Kaizen
- Selecting the right team for the Kaizen
- Identify the root cause not just symptoms
- Challenge everything and seek supporting data and evidence
- Define the measures by which success and improvement will be measured
- Implement the measures for improvement
- A good plan implemented rapidly now is better than a perfect plan implemented later
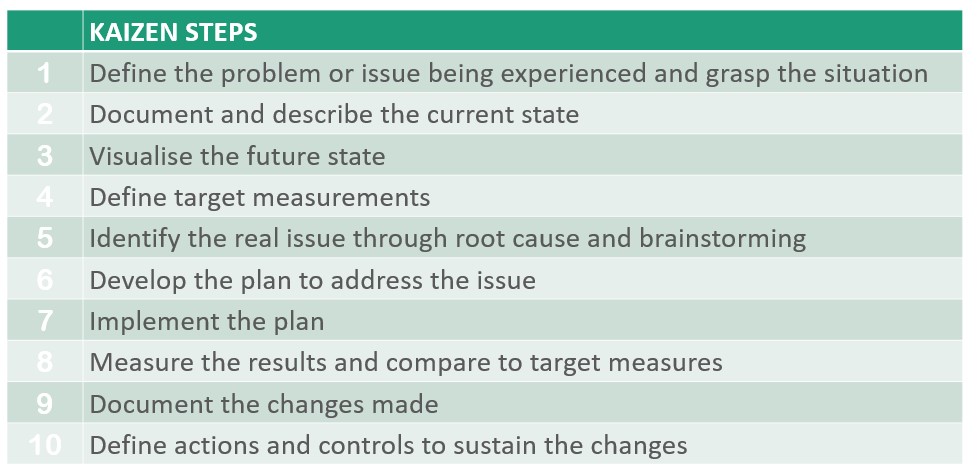
Six Sigma
Six Sigma uses data driven methods and tools for problem solving to remove variations in process inputs and outputs that effect product or service quality and customer satisfaction.
DMAIC is a data driven quality framework for improving processes, executed in the sequence below.
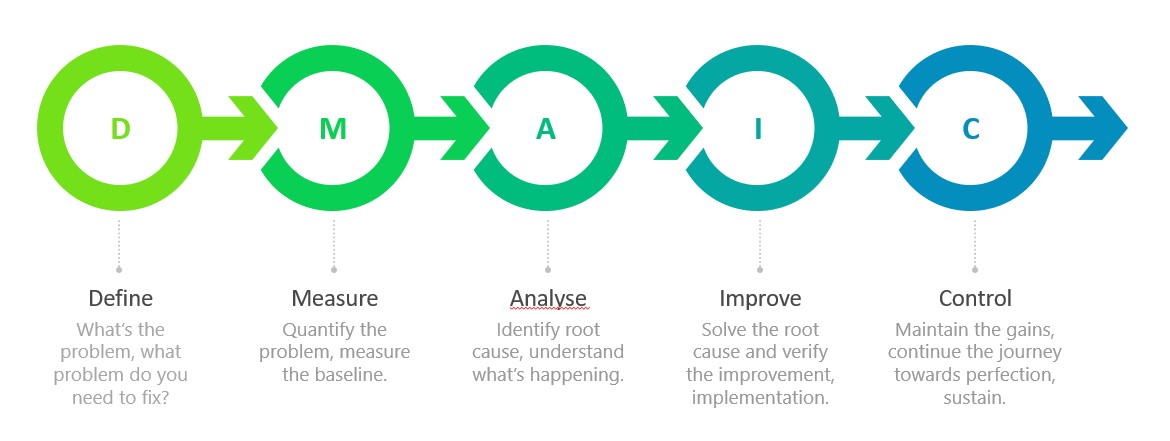
DMADV is another data driven quality framework used for designing processes, services and products.
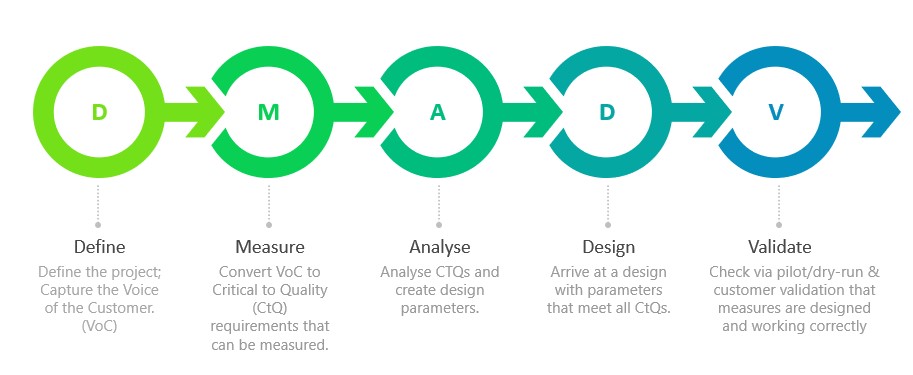
The lean sigma methods and tooling combined with project management and change management best practices will enable your next strategic business improvement project to deliver sustainable results.
Purpose, Process, People (lean.org)
Womack and Jones (Lean Thinking) recommend that managers and executives embarked on lean transformations think about three fundamental business issues that should guide the transformation of the entire organization:
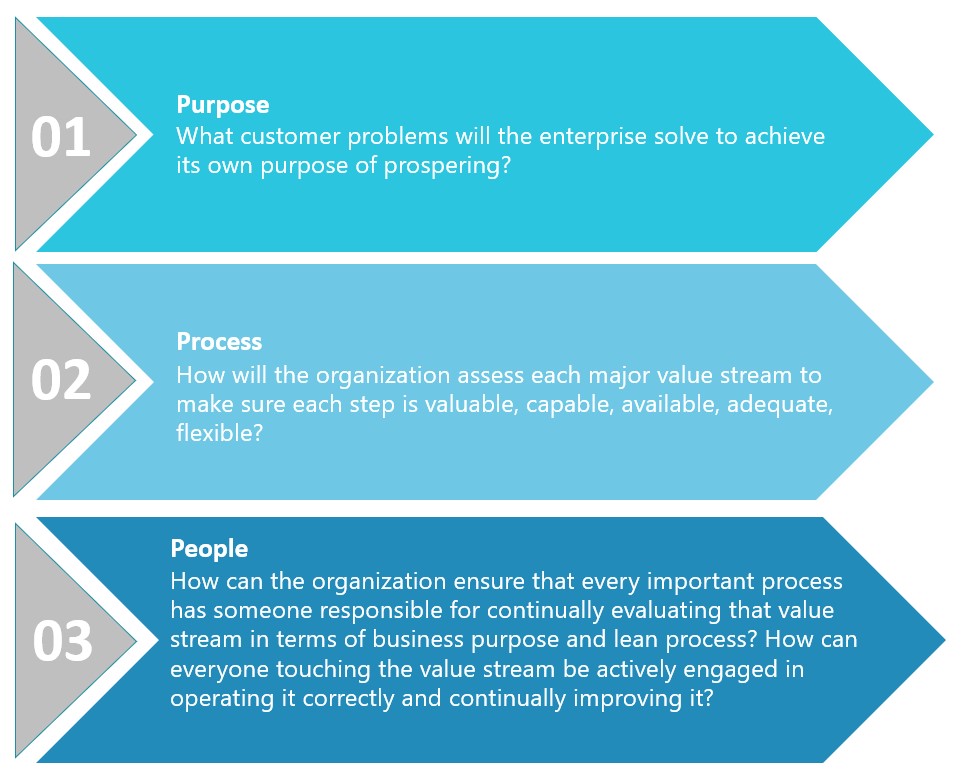
At Clarion we can support you to improve processes and implement change. If you would like to discover more on how you can enable your business or organisation to excel in the race to adapt to constant change then contact us to find out how we can help you.
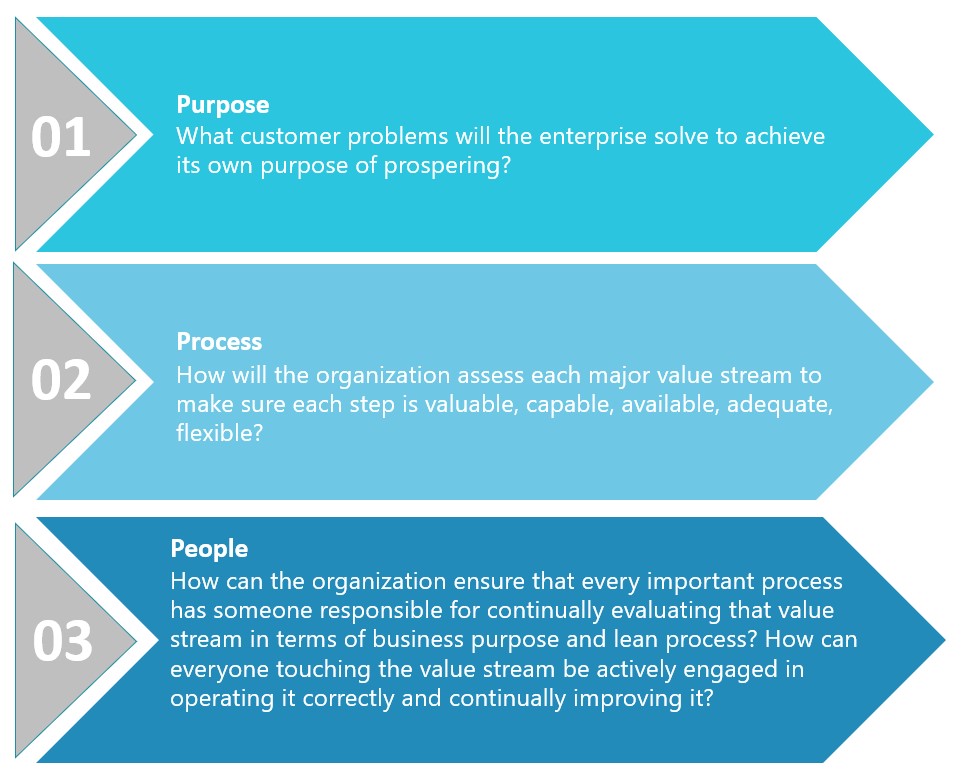